Apr 29, 2025
How AI-Powered Predictive Maintenance Is Solving One of Manufacturing’s Biggest Problems
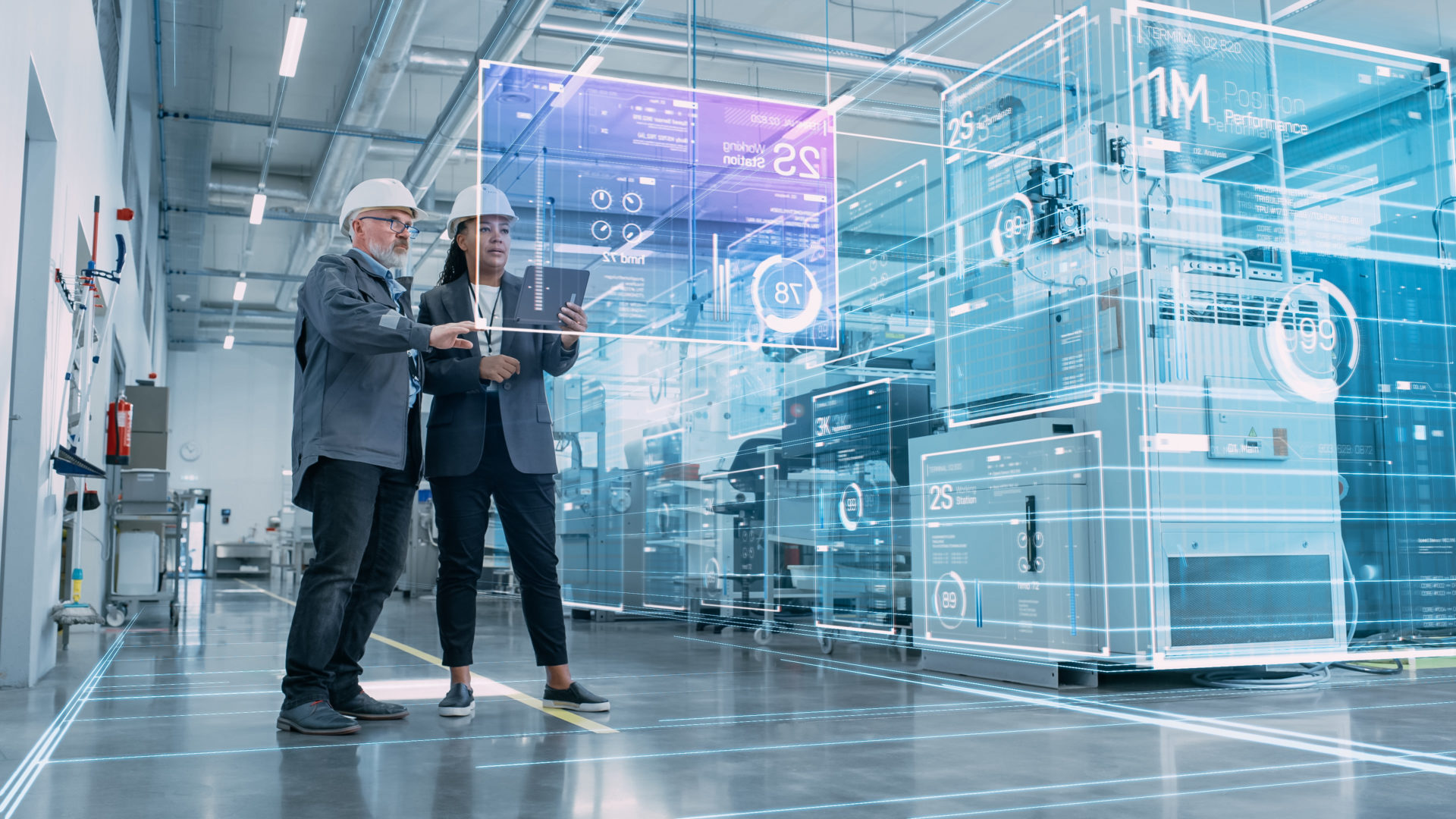
In today’s complex and fast-paced manufacturing landscape, unplanned downtime is a critical issue across industries — from electronics and industrial machinery to food processing and consumer goods. Despite advanced machines and automation, many manufacturers still grapple with equipment failures that halt production, disrupt delivery schedules, and increase costs.
The traditional approach of reactive or time-based maintenance simply can’t keep up with the demands of modern, data-intensive manufacturing. But one solution is turning the tide: AI-driven predictive maintenance.
The Manufacturing-Industry Challenge: Downtime, Disruptions, and Rising Costs
Manufacturers today face a perfect storm of operational pressures:
- Aging equipment and complex machinery that require increasingly specialized maintenance
- Limited visibility into machine performance, especially across dispersed production lines
- Supply chain delays, which make any unplanned downtime even more damaging
- Rising energy and raw material costs, putting profitability under pressure
- Sustainability and efficiency goals that demand smarter resource usage
Together, these issues create a scenario where every unexpected breakdown not only affects the bottom line but also undermines operational resilience and customer trust.
The Solution: Predictive Maintenance Powered by AI and Data Transparency
To overcome these challenges, modern manufacturers are taking bold steps: deploying AI-powered predictive maintenance across their operations, by implementing a fully integrated, data-driven solution that transforms how monitoring, maintenances, and production asset-monitoring work.
Here’s how the transformation can happen:
1. Sensor-Driven Monitoring
Industrial IoT sensors are needed on key equipment, constantly tracking parameters like temperature, vibration, pressure, and power consumption.
2. AI & Machine Learning Algorithms
Advanced models analyze sensor data to detect subtle patterns and anomalies that signal potential failures — often days or weeks before a breakdown would normally occur.
3. Software-Defined Manufacturing (SDM)
By shifting to a software-defined manufacturing approach, manufacturers can achieve full data transparency across their operations. Real-time machine data is centralized, accessible, and actionable — enabling better decision-making at every level.
4. Predictive Maintenance Workflows
Maintenance teams received alerts and insights, enabling precise, proactive interventions. Rather than over-maintaining or reacting too late, they can optimize scheduling and avoid costly production disruptions.
The Results:
This AI-driven transformation can deliver significant operational gains of up to:
✅ 40% fewer equipment failures
✅ 25% increase in production efficiency
✅ ~30% cost savings in maintenance and operations
✅ 10% reduction in material waste
✅ 20% energy savings through optimized machine usage
Why It Works: From Reactive to Intelligent Manufacturing
Predictive maintenance isn't just a new tool — it’s a strategic enabler for manufacturers aiming to remain competitive, resilient, and sustainable. By combining real-time data with intelligent algorithms, it allows organizations to:
- Minimize unexpected downtime
- Extend the life of expensive equipment
- Optimize resource usage
- Reduce waste and environmental impact
Whether you're in automotive, machinery, electronics, food & beverages, or pharmaceuticals, the benefits are clear: AI-powered operations mean more uptime, less waste, and better margins.
Ready to Make Your Factory Smarter?
As manufacturing continues to evolve, digital solutions like AI will define the leaders from the laggards. Predictive maintenance is one of the fastest and most impactful ways to begin that journey.
Curious how your factory could benefit from software defined production?
Our team can help assess your readiness and identify the right path to AI adoption.